Project Description
A Case Study on the Integration of Industrial AI:
Optimization of the Nickel and Copper Milling Process
The Problem
Integral to the success of this global mining company’s nickel and copper operation was the intricate milling process – a process which, if further optimized, held the potential to significantly increase profits from improved nickel and copper separation. The company was looking to integrate an AI tool to identify optimal control settings to which the challenge fell on LityxIQ.
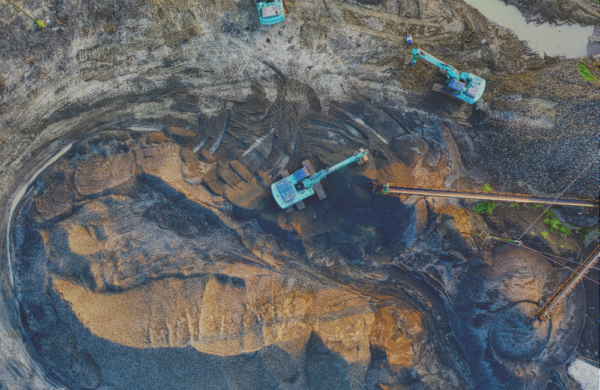
The Primary Objectives
✔ Minimize the percentage of Nickel (%Ni) in Copper (Cu) concentrate and the percentage of Copper (%Cu) in Nickel (Ni) concentrate during single grinding line, steady-state operations.
✔ Control for the fluctuating mix of the ore being processed.
✔ Navigate the dynamic between %Ni and %Cu levels where a decline in one results in an increase in the other. Not one-to-one though.
✔ Discover the best combination of process controls and settings for superior results.
✔ Build a virtual environment for identifying opportunities to optimize processes, reduce waste and increase profitability.
An exhaustive analysis of hourly processing data from a recent two-month period along with 2,148 assay records became the foundation of this quest.
How We Solved It
With the integration of LityxIQ’s powerful AI platform and the collaboration of our seasoned experts, a dual methodology was adopted to generate actionable insights:
- Golden Moment Approach: Identification of repeatable peak performance moments and the DNA that created those moments. By decoding the control settings during these golden moments, the path was laid out to recreate them for consistent, optimum results.
- Simulated Data Approach: Simulation of key control combinations that may or many not have been used based on accurate modeling of the milling process. This virtual twin sandbox enabled the team to predict outcomes and optimize processes, while avoiding potentially costly mistakes that can occur when testing in a production environment.
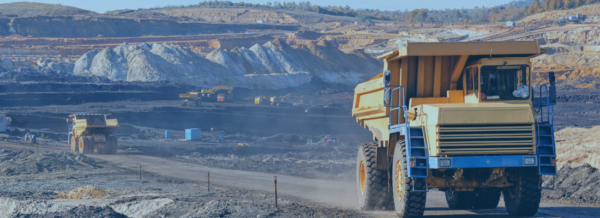
Through the seamless synergy of LityxIQ’s Data Manager, Insights, and Predict and Optimize modules, the colossal task of managing and deciphering the client provided datasets became streamlined. This precision facilitated an in-depth exploration of pivotal trends, relationships, and the construction of impactful models.
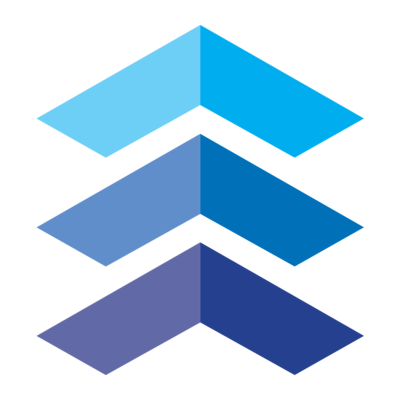
Predicted Outcomes
500% Reduction of %Ni in Cu Concentrate
320% Reduction of %Cu in Ni Concentrate
Probability of hitting the top-priority target value amplified by 337%
Achieving the secondary desired outcome saw a boost of 35%
Conclusion
This initiative, powered by the LityxIQ platform, highlighted the significant advantages of implementing machine learning in refining the milling process for mining operations. Additionally, the speed and ease to construct a digital twin environment through LityxIQ creates a competitive advantage, increases operational efficiencies, and accelerates decision-making.
The results obtained are not merely statistics but represent the forward strides the industry can make. By pinpointing optimal control settings, the presence of undesired elements was substantially reduced, presenting a roadmap for future enhancements.
Get Started
with Lityx
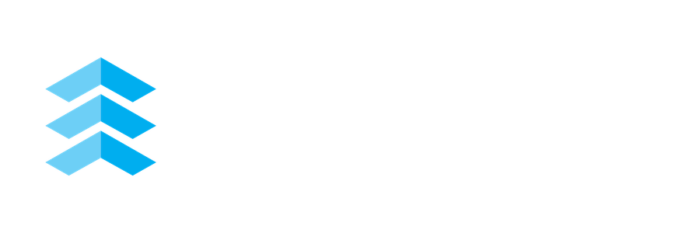